The ball screw pair was invented as early as the end of the 19th century, but it has not been practically applied for a long time, because it is too difficult to manufacture. The world's first ball screw pair was the US General Motors Saginaw plant, which used the ball screw pair on the steering mechanism of the car. In 1940, the United States began mass production of ball screw pairs for automotive steering mechanisms. In 1943, the ball screw pair began to be used on aircraft. The appearance of precision thread grinders has made the ball screw pair a big leap in precision and performance. With the development of CNC machine tools and various automation equipment, the research and production of ball screw pair has been promoted. Since the 1950s, in industrially developed countries, ball screw manufacturers have sprung up, such as: WARNER-BEAVER, GM-SAGINAW, USA; ROTAX, UK; NSK, TSUBAKI, Japan Wait. As early as the late 1950s, China began to develop ball screw pairs for program-controlled machine tools and CNC machine tools. For more than 40 years, the ball screw pair has been widely used in machinery, aerospace, aviation, nuclear industry and other fields due to its high efficiency, high precision and high rigidity. Ball screw pairs are now the preferred component for mechanical transmission and positioning. The development of the ball screw pair is mainly in the following aspects. 1 Types of ball screw pairs
Due to the increasing popularity of the use of ball screw pairs, the use of the field continues to expand, the requirements for the ball screw pair are also increasing, the ball screw pair of the ordinary specifications has been far from meeting the requirements of use, such as aerospace, small precision Test equipment, electronic equipment, and semiconductor devices basically require a miniature ball screw pair having a nominal diameter of d0 ≤ 12 mm and a lead Ph of 0.5 to 2.5 mm. NSK Corporation of Japan has developed the world's smallest lead miniature ball screw pair with a nominal diameter of d0=4mm and a lead of Ph=0.5mm. Semiconductor plug-in devices, small robots, etc. require miniature lead balls and screw pairs to meet high-speed drive requirements.
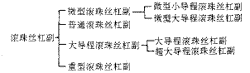 Figure 1 Ball screw sub-classification |
With the development of mechanical products in the direction of high speed, high efficiency and automation, industrial robots, CNC forging machines, machining centers and mechatronics automatic machines, etc., the feed drive speed is continuously improved, and the emergence of large lead ball screws is satisfied. High speed requirements. Japan NSK Company has developed a nominal diameter × lead: 15mm × 40mm, 16mm × 50mm, 20mm × 60mm, 25mm × 80mm super large lead ball screw pair, fast feed speed of 180m / min. The ball screw pairs are classified as shown in Figure 1. There is no uniform classification of ball screw pairs in domestic and foreign literatures, but countries generally classify according to the following principles. Ordinary ball screw pairs generally refer to nominal diameter d0=16~100mm, lead Ph=4~20mm, The helix angle is φ<9°. The miniature ball screw pair refers to a ball screw pair with a nominal diameter of d0 ≤ 12 mm. For a ball screw pair with a lead Ph ≤ 3 mm, it is called a miniature small lead ball screw pair, and a ball screw pair with a screw angle φ > 9° is called a micro large lead ball screw pair.
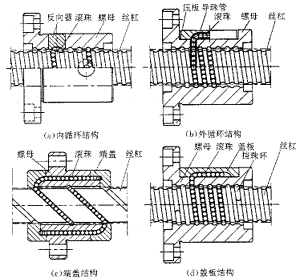 Figure 2 Main structure of the ball screw |
The large lead ball screw pair refers to the ball screw pair with the nominal diameter d0≥16mm, the helix angle of 17°≥φ>9° or the lead d0≤Ph≤d0. For the helix angle φ>17°, it is called super large guide. Cheng ball screw pair. The heavy duty ball screw pair refers to a ball screw pair with a nominal diameter of d0 ≥ 125 mm. 2 Ball screw substructure
The structure of the ball screw pair is traditionally divided into an inner circulation structure (represented by a circular reverser and an elliptical reverser) and an outer circulation structure (represented by a cannula). These two structures are also the most commonly used structures. There is no essential difference between the two structural properties, except that the inner loop structure has a small installation and connection size; the outer loop structure has a large installation and connection size. At present, there are more than 10 types of ball screw pairs, but the more commonly used ones are (Fig. 2, attached table): inner circulation structure; outer circulation structure; end cover structure; cover structure. The shape of the inner loop structure inverter is various, but the commonly used shapes are circular and elliptical. Since the circular ball has a short reverse passage, it is not as smooth as an elliptical structure. Now, the best inverter structure is an elliptical inner channel structure. Since the ball reversal does not pass through the screw tip, similar to the outer loop structure, the screw tip chamfering error is eliminated to the ball reverse. influences. However, due to the complexity of the manufacturing process, the promotion of this structure has been affected.
Comparison of structural characteristics of the attached ball screw species | Characteristics | Number of cycles | Nut size |
Number of turns | Number of columns |
Inner loop structure | A ball circulation loop is formed by an inverter, and each of the inverters constitutes a ring of balls. Therefore the load is small. Suitable for miniature ball screw pairs and ordinary ball screw pairs. | 1 | 2 or more columns | small |
External circulation structure | The ball circulation loop is formed by the cannula, and each cannula has at least 1.5 turns of the ball chain, so the load is large. Adapted to small lead, general lead, large lead and heavy ball screw pair. | 1.5 or more | 1 or more columns | Big |
End cap structure | The ball circulation loop is formed by the end caps at both ends of the nut, and each loop has at least one ring of ball chains, and the bearing is large. Adapted to multi-head large lead, super large lead ball screw pair. | 1 or more | 2 or more columns | small |
Cover structure | The ball circulation loop is formed by the cover plates, one cover for each nut, and each cover plate constitutes at least 1.5 turns of the ball chain. Adapted to the miniature ball screw pair. | 1.5 or more | 1 | in |
3 Ball screw precision
In the past, in order to obtain high positioning accuracy, it was mainly achieved by improving the accuracy of the ball screw copy body. Therefore, the lead accumulation error of the ball screw was required to be high, which made it difficult to manufacture the ball screw pair, making the ball The production cost of the lead screw pair is increased. In particular, the high-precision ball screw pair can only be achieved by CNC thread grinding machine or laser feedback thread grinding machine. With the continuous development of science and technology, people have mastered the numerical control compensation technology. Therefore, high precision positioning accuracy can be obtained without requiring a highly accurate ball screw pair. In order to meet the requirements of CNC compensation technology, the international standard ISO3408-3-1992 and the ministerial standard JB3162.2-92 all require the stroke variation of the ball screw pair, such as the amount of stroke within the effective stroke, any 300mm stroke The amount of change in stroke and the amount of change in stroke within 2Ï€ radians. The purpose is to control the linearity of the ball screw secondary stroke error, that is, the ball screw secondary stroke error linearization. Create conditions for CNC error compensation. 4 Ball screw performance
With the continuous development of science and technology, people's requirements for ball screw pairs are getting higher and higher. In order to achieve high positioning accuracy and smooth operation of mechanical products, this requires that the ball screw pair not only has high precision, And the operation is stable and there is no blockage. Whether the ball screw pair operation is stable depends mainly on the variation of the pre-tightening torque of the ball screw pair. The ball chain movement of the ball screw pair has different fluency at different speeds. Therefore, the pre-tightening torque of the ball screw pair Not the same. The international standard ISO 3408-3-1992 and the ministerial standard JB3162.2-92 specify the tolerance of the ball screw pair pre-tightening torque at a speed of 100 r/min. Due to machining errors, such as the inconsistent total length of the ball screw, the lead error of the lead screw and the nut, the tooth profile error of the lead screw and the nut, and the roughness of the thread raceway, etc., the ball screw pair The dynamic pre-tightening torque is not constant over the entire length of the screw thread, which directly affects the stability of the drive system and thus also the positioning accuracy of the ball screw pair. Therefore, the magnitude of the ball screw pair pre-tightening torque variation is an important indicator reflecting the performance of the ball screw pair. In recent years, people began to pay attention to the amount of pre-tightening torque variation of the ball screw pair. In the past, people only paid attention to the comprehensive stroke error curve of the ball screw pair, and now also pay attention to the curve of the ball screw pair pre-tightening torque. . Because of these two curves, the performance of the ball screw pair can be well reflected. In order to meet the above requirements, Beijing Machine Tool Research Institute has developed a ball screw pair integrated stroke error measuring instrument and pre-tightening torque measuring instrument. Using modern measuring methods and high-precision sensors, the travel error curve and pre-tightening torque curve can be displayed in real time during the measurement process, and a complete measurement report can be printed to provide a reliable measure of the quality of the ball screw pair assembly. Detection means. With the development of CNC machine tools, "high speed and high efficiency" has become the goal pursued by various manufacturers. For high-speed drive and positioning components, linear motors have been introduced abroad, and they have been used in machining centers. The rapid feed rate is above 160m/min. Up to 4g, it poses a serious challenge to the ball screw pair. However, due to the high cost of the linear motor, the complicated control system, and the need to take measures to solve the shortcomings of magnet attracting metal chips, strong magnetism to human body and heat, it has been difficult to popularize in recent times. The ball screw pair is still the most preferred choice for high-speed drive now, and most of the high-speed machining centers in foreign countries still use the ball screw pair. In order to achieve the purpose of high-speed drive, the design of the motor speed (maximum motor speed up to 4000r / min), while using a large lead ball screw pair, lead up to 32mm. For example, the Japanese Mazak company uses the ball screw pair on the FF660 machine tool, the machine tool moves at a speed of 90m/min and the acceleration reaches 1.5g. In the past, I was worried about the influence of the large lead ball screw drive on the accuracy of the machining center. The lead was designed to be Ph ≤ 10 mm. With the advancement of science and technology, it can be seen from the 1999 Japan International Machine Tool Show that design and research nowadays most high-speed machining centers use large lead ball screws. The main problems of the ball screw pair in high-speed driving are: noise, temperature rise, and accuracy. The main causes of the noise of the ball screw are: the smoothness of the ball in the circulation loop, the collision between the balls, the roughness of the raceway, and the bending of the lead screw. The temperature rise of the ball screw pair is mainly caused by the friction between the ball and the screw, the nut, the reverser and the friction between the balls. To solve the above problems, we should first start with the structural design of the ball screw pair and take measures for the existing problems; on the other hand, solve the problem from the process, improve the intrinsic quality of the product through a reasonable process flow; select the appropriate ball screw pair Pre-tightening torque; reducing the variation of the pre-tightening torque of the ball screw pair, so that the ball screw pair can meet the requirements of high-speed driving. In short, with the continuous development of the society, users are increasingly strict with the requirements of the ball screw pair, and the requirements are also diversified, prompting the ball screw production plant to continuously improve product quality and develop new varieties to meet the needs of users. Wardrobe Cabinet Handle
Wardrobe Cabinet Handle,Thickened Solid Door Handle,Pure Copper Door Handle,Minimalist Wardrobe Invisible Handle
Guangzhou Junpai Hardware Co., Ltd , https://www.gdjhfurniture.com