Analysis and elimination of water leakage fault of submersible pump
1. Before using the submersible pump, check the cable, switch, electric shock protector, etc. The switch and other electrical appliances should work normally, the cable is not damaged, and pay attention to carefully identify the cable. The yellow and green two-color lines are grounded to prevent electric shock and electric shock.
2. The submersible pump should check the insulation resistance of the submersible pump at intervals of 0.5MΩ before use. If it does not meet the requirements, it should be dried.
3. Regularly check the submersible pump drain hole and drain hole. Tighten if there is no abnormality.
4. When the submersible pump enters the water or the water, the TSWA horizontal multistage pump must first cut off the power supply, and then pull the rope on the lifting ring, and the cable can be pulled absolutely.
5. The submersible pump should not be buried in the river mud. If there are more water and debris in the water, the submersible pump should be placed in the basket or the basket, and then the basket or basket should be placed in the water.
6. After the submersible pump is working for 300h, it is necessary to carry out the sensitive water inspection. If the water or oil-water mixture discharged is less than 25mL, it can be used continuously, otherwise it is necessary to check whether the block and rubber seal are damaged.
7. When the submersible pump is tested outside the water (for example, to determine the steering), it must not exceed 5 minutes to prevent the motor from burning out.
Submersible pump leaking fault
Most of the submersible pump leakage faults are caused by aging and wear of the sealing device. In addition to replacing the new seals, the following simple elimination methods can be adopted. The rubber seal ring in the nylon seal seat of the submersible pump is worn out, and the seal ring can be taken out and replaced. Position mounting, such as the fastening spring on the seal loses its elasticity or breaks, remove the spring and tighten with a wire or wire of appropriate diameter.
The submersible pump seal ring loses its elasticity due to long-term use. At this time, the seal ring can be taken out, and then a piece of paper or cloth with a thickness of 0.3 to 0.5 mm is cut into a groove slightly larger than the original seal ring. Finally, Install the original seal. The first seal ring of the submersible pump is severely worn. The nylon seal ring can be taken out, and the asbestos rope coated with butter is wound on the stainless steel sleeve to fill it slightly higher than the original nylon seat, then filled with butter, and then the nylon seat is tightened with bolts. Compaction.
The submersible pump seal box and the cast iron seal ring lose their elasticity. The seal ring can be taken out from the cast iron tank. Find a piece of cardboard with a thickness of six to one millimeter and cut it into the same size, pad in the groove, and then seal it. Put in the circle. If the rubber seal of the submersible pump oil hole is damaged, you can find a piece of tape, cut it into a hole slightly larger than the bolt, add a flat pad on the upper side, and put it in the oil hole of the bolt together. (Source: Sealing Technology Network)
Aramid packing
Scope of application: There are granular fluids and their media, steam, organic solutions, acids, alkalis, etc., applied to the sealing of machinery, pumps, valves, pipes, containers, etc. used in fluid conveying equipment.
Features: The filler has excellent lubricity and wear resistance. The most outstanding performance is high strength, high grinding capacity, good chemical resistance, high rebound, low cold flow and easy disassembly. It is especially suitable for dynamic sealing parts containing solid particle media.
Technical parameters: Temperature: -100 ° C ~ +300 ° C
Pressure: 35MPa
Chemical resistance: PH value 2-13
Graphite packing adaptability range: sealed hot water, high temperature, high pressure steam, heat exchange medium, hydrogen, ammonia, organic solvent, hydrocarbon, cryogenic liquid, etc., except for a few strong oxidizing media, used in petroleum, power plants, chemical industry Sealing of valves in industrial fields such as steel mills.
Features: The filler has high mechanical strength, and has strong versatility, good flexibility and high strength, and has a protective effect on the shaft. In the general combination of packing and packing, the sealing performance is more perfect and safer, and it is the most effective sealing element to solve the problem of high temperature and high pressure sealing.
Technical Parameters:
Temperature: 800 ° C
Pressure: 35MPa
Chemical resistance: PH value 0-14
PTFE packing range: It is made of raw material belt. It is suitable for packing and sealing of valves, kettles and pumps under corrosive medium conditions in chemical, pharmaceutical, food, petrochemical and electric power industries.
Technical Parameters:
Temperature: -200 ° C ~ 280 ° C
Line speed: 20M/S
Pressure: 2MPa 15MPa
Chemical resistance: PH value 0-13.
The ceramic fiber packing is woven with high-quality ceramic fiber, which has good wear resistance and high temperature resistance. Widely used in high temperature sealing parts such as steel mills and petrochemicals. Ceramic fiber packing can be used as an alternative packing for asbestos packing, with outstanding results.
SUNWELL P803P -- Dip PTFE ceramic fiber packing. The ceramic packing after being impregnated with the tetrafluoro emulsion has a lower friction coefficient and a higher structural strength;
SUNWELL P803S -- Metal reinforced ceramic fiber packing. The metal fiber is added into the ceramic fiber to make the ceramic fiber packing have better wear resistance and improve the pressure resistance;
SUNWELL P803R -- Silicone core ceramic fiber packing. The silicone core is added inside the ceramic fiber packing to make the ceramic fiber packing have better resilience and the sealing cavity is more tightly combined.
Outstanding performance:
1. Low maintenance costs and easy control;
2. Good structural strength and high temperature resistance;
Ceramic fiber packing is suitable for high temperature, high pressure machine, pump and valve sealing equipment: metal processing, boiler door, high temperature furnace door, high temperature, high pressure machine, pump, valve industry: can be widely used in chemical, electric power, paper , food, pharmaceutical and other industries media: clean fluid or slurry, brine, emulsion, grease, hydrocarbons, solvents, pulp.
Pressure 3-20Mpa
Temperature (Temperature) 800-1200 ° C
Ph range (PH range) 3~14
Linear speed is 12 m / s m / s.
3. Ceramic fiber packing is an economical packing, which can be used as a substitute for asbestos packing in areas where asbestos is not allowed.
Hebei Innovation Sealing Material Co., Ltd.
Mobile phone
phone
Website:
Contact: Business Manager
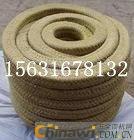
Musk Xylene is a Synthetic Musk fragrance which mimics natural musk.
It has been used as a perfume fixative in a wide variety of consumer products, and is still used in some cosmetics and fragrances.
Musk xylene was once the most widely used of the "nitro-musks", but its use has declined sharply since the mid-1980s due to safety and environmental concerns, and musk xylene is a useful example of the lowest level of such risks which need to be taken into account.
Musk Xylol,Musk Xylenemusk Xylol ,Farwell Musk Xylol ,Musk Xylol Synthetic
Gan Su Original Flavor Co.,ltd , http://www.muskxylol.nl