Â
Thank you very much for choosing the grinding machine produced by our company. In order to get good results, I hope you can carefully understand the following questions before using the sharpening machine officially:
First, check carefully whether you have selected the corresponding sharpener according to your needs.
Our company has manufactured a variety of grinding machines according to the needs of users. The sharpening machines used are different for different cutting precision. If you have difficulty in selecting, please let us know the sales engineers of the company, they will provide you with appropriate help.
two, Â How to sharply sharpen the blade you bought
The cutting performance of mechanical inserts depends to a large extent on the sharpening quality of the insert. The quality of the sharpening depends on the choice of sharpening equipment, the choice of grinding wheel, the choice of sharpening amount and the reasonable sharpening process.
1 sharpening equipment - selection of sharpening machine
For the cutting of the mechanical inserts for long cutters, we propose that you use the grinding head-type spindle sharpener with the grinding wheel end face sharpening shown.
In order to avoid burn grinding surface during sharpening, please adjust the grinding head axis, which is the working surface of the grinding wheel inclined 10 ˊ to 30 相对 relative to the sharpening surface .
If you use a horizontal shaft sharpening machine for grinding, you must have a master with rich experience to operate, because the angle of the knife edge is difficult to master. According to the State Press and Publication Board: From July 1, 2002, have banned production of Horizontal Grinder.
2 grinding wheel selection
( 1 ) Abrasives for grinding wheels: We propose that you use white corundum (code WA ) because this kind of abrasive is not easy to heat when sharpening sharply, and then choose brown corundum (code OA ) or chrome corundum (code PA ).
( 2 ), the size of the grinding wheel: We propose that you choose 46 # ~ 60# . The abrasive grains of the grinding wheel are too thick, the sharpness of the sharpening is not up to the requirement, and the cutting edge is easy to be cracked; when it is too thin, the surface of the sharpening is easily burned, and the sharpening efficiency is also low.
( 3 ), the hardness of the grinding wheel: We suggest that you choose one of the three types of H , J , and K that are softer . If the grinding wheel is too hard, it will burn the surface of the sharpening surface; while the grinding wheel is too soft, the grinding wheel will quickly consume waste. The hardness of the grinding wheel should be inversely proportional to the hardness of the material to be ground. That is to say, if you choose the blade with a high blade hardness, the grinding wheel with H hardness should be used . Otherwise, the grinding wheel with K hardness should be used.
( 4 ), the adhesive of the grinding wheel: We propose to use the resin adhesive (code B ). If you use a cup wheel, you can also use a ceramic adhesive (code V ). When using a resin-coated grinding wheel, please be careful not to use alkaline cutting fluid at the same time, otherwise the adhesive will be broken down and destroyed, which will affect the robustness of the grinding wheel.
3 recommended sharpening amount
( 1 ), the peripheral speed of the grinding wheel: V = 15 ~ 25m / s ( m / s )
( 2 ) The relative movement speed of the grinding head and the workpiece: Vt=5 ~ 15 m/min ( m / min )
( 3 ), grinding head feed: grinding depth feed is related to the width of the sharpened bevel (slash surface), wide and less feed, narrow multi-feed. Generally, the initial coarse grinding is mastered at 0.012mm/str ( mm / stroke ) , and the fine grinding is mastered at 0.005 mm/str ( mm / stroke ) .
4 sharpening process requirements
( 1 ), grinding wheel rotation direction:
The two directions of rotation of the grinding wheel,
a ) indicates that the grinding wheel rotates against the cutting edge, which will cause a small gap in the cutting edge. This phenomenon is particularly prominent for high speed steel.
b ) indicates that the grinding wheel rotates along the oblique opening, and the small gap described above rarely occurs.
However, when the selected grinding wheel is too hard or the grinding is too smooth, the cutting edge is more likely to have a small gap. We propose that you adjust the grinding wheel rotation direction b )
( 2 ), choose the appropriate wedge angle (knife angle): the wedge angle (knife angle) is the main angle affecting the cutting performance of the mechanical blade, the angle of the size depends mainly on the material to be cut, when you do not specify the requirements, The blade angle of the blade provided by the manufacturer is made according to the general 22 ° requirements. Depending on the material to be cut, the angle of the blade may be as long as 17 ° or as large as 28 °. The angle to be used depends on the actual situation. Here we introduce you to a groping experience: cutting soft materials - small angles, hard materials - large angles.
( 3 ) Use a certain pressure of cooling liquid: When sharpening, the coolant must be used in the sharpening area, so that the blade can be fully cooled during the whole grinding process, otherwise the grinding surface will be overheated and the cutting edge will be lost. For cutting ability, usually use No. 1 metal emulsified cutting fluid or D15 anti-mold rust-proof emulsion. The coolant should be directly injected into the contact part of the grinding wheel. The fully pressurized coolant is not only used for cooling work contact. Point "take away" the heat generated by the grinding, and also have a cleaning wheel to prevent the accumulation of dirt.
Directly using water as the coolant is unfavorable for the grinding of the blade. It will cause dirt on the surface of the blade to appear quickly, and the grinding wheel will also become sticky. The coolant prepared by adding certain substances can take away the grinding. Dirt and prevent the grinding wheel from sticking.
( 4 ) Master the correct sharpening method: For the user, the sharpening edge is only the beveled part, and some users are for some purpose. In order to make the cutting front (large plane) of the knife have a concave shape, grind it by itself. Cutting the front is not advisable.
We believe that to grind a knife, we must pay attention to three steps to achieve the goal, these three steps are: rough grinding, fine grinding and finishing protection.
coarse grinding
The purpose of the rough grinding is to remove the defects of the cutting edge and form a preliminary shape of the cutting edge angle, so that a relatively large feed amount can be used. The temperature at the point of contact between the blade and the grinding wheel can still be tolerated by quietly reaching 200 °C. Remember: Do not give the ground surface a pale yellow or even blue-blue spots. The occurrence of discoloration spots indicates that the temperature has exceeded 200 °C, and subsequent grinding can remove these discoloration spots, but the defects on the blade still exist, which affects the performance of the blade.
fine grinding
Fine grinding is the main step of the whole sharpening. Uniform micro-feeding and sufficient cooling are two key points worth noting. When the ground surface is silver-gray and there is a tiny burr in the blade back direction, fine grinding is even fine. ended.
Photo-curing
Photo-finishing refers to the fact that the grinding wheel or the tool holder can travel several times without the feed amount, so as to improve the straightness of the cutting edge and the self-measurement of the sharpening surface. Generally , the blade of 1 meter length passes through 7 ~ 8 trips can achieve this goal. For longer blades, it may take more than 20 strokes to meet the requirements.
Three-use oil stone for fine polishing of the cutting edge can improve the cutting performance of the blade
It is impossible to obtain an absolutely sharp edge with a grinding wheel sharpening method. In general, the width of the blade edge milled by the grinding wheel is f=0.005 to 0.008mm . In order to improve the quality of the sharpening and eliminate the small burrs on the cutting edge, the sharpened blade also needs fine polishing with oil stone to obtain a sharper edge. First, you need to use a soaked oil stone to grind the cutting edge without pressure to remove the burrs from the grinding machine.
We have found that some operators use a wooden strip to remove the burrs. This is extremely inappropriate because it will pull the burrs hard and the edges will be jagged. When you use oil stone for the first time, you may not be used to it or worry about the instability of the blade and affect the straightness of the cutting edge. Then you can only use the white long paper to gently pull it on the cutting edge. This is more reasonable than using the wooden strip. After completing the above work, you will put the oiled cleaned oil stone on the rake face as shown.
In the continuous rotation movement method, pay attention to the operation of the front rake face, the pressure should be small, first use W10 oil stone, then use W5 ~ W1 fine particle oil stone or natural oil stone processing. The fine knives must be flattened, and the tilting and swaying shown should not occur, otherwise the blade will be curled.
The back of the blade is polished in the same way, but the oil stone is tilted slightly to the outside by <1 ° (the indication has been exaggerated for actual operation), and the excessive tilt will make the blade dull.
Fourth learn to identify grinding defects
1. When using it, a blade suddenly collapses. If there is no hard foreign object encountered, the more common situation is caused by the temperature being too high during grinding and “burning out†the blade. After the grinding temperature is too high, the stain on the surface can be worn away, but the damage inside the metal cannot be worn away. There is nothing visible on the surface of the naked eye. Once it is used, it will be revealed.
2 , the edge is a little yellow spot, the surface of the object being cut has a knife flower is the knife too soft?
When this occurs are mostly due to overheating, excessive local temperature to 300 ~ 350 ℃, here a metallic material generated cracks caused by shrinkage, does not mean the absence of invisible, the hardness of these regions must also have significant The decline, the inferior cutting will become inevitable.
Shown is the same situation seen by the naked eye before and after acid corrosion of the same part of the same knife.
Just can see the color change without seeing the crack,
It shows that after the corrosion, the original hidden crack is revealed.
Five receiving sharpening technology training
  The person who uses the blade must understand that the use of the blade is a big factor. It is the quality of the sharpening. It is very important to learn the sharpening knowledge and accumulate the experience of sharpening. To this end, our company organizes sharpening classes from time to time to carry out relevant technical training. If you are willing to participate in technical training, you may wish to tell us the sales department of the company. We will inform you to discuss it together.
Six-blade sharpening angle reference table
Type of cut | angle |
Soft paper (cigarette paper, carbon paper, filter paper, blotting paper) | 16 0 |
Industrial fabrics, varnishes and fabrics | 16 0 |
Hard and dense paper (copper paper, writing paper, type paper) | 19 0 -20 0 |
Insulating paper, transparent paper, polyester paper, fiberglass fabric | 19 0 -24 0 |
Cardboard, plywood | 20 0 -30 0 |
Aluminum, tin, zinc and other metal films | 19 0 |
Attachment 1 , Reference: Tianming Grinding Machine Technical Support Center   Http://
Attachment 2 , cited website: China Grinding Machine Network   Http://
Attachment 3 , English information: China grinding machine supplier   Http://
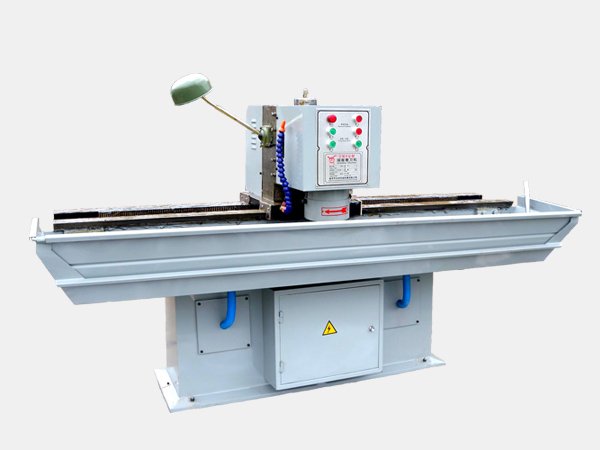
EVA Twin Colors Building Blocks is consist of all kinds of twin colors foaming blocks. Made from Eco-friendly, closed cell, non-smell and non-toxic Eva Foam material, passes ASTM and EN71 certificates, the safety of this product is the last thing needs to be worried.
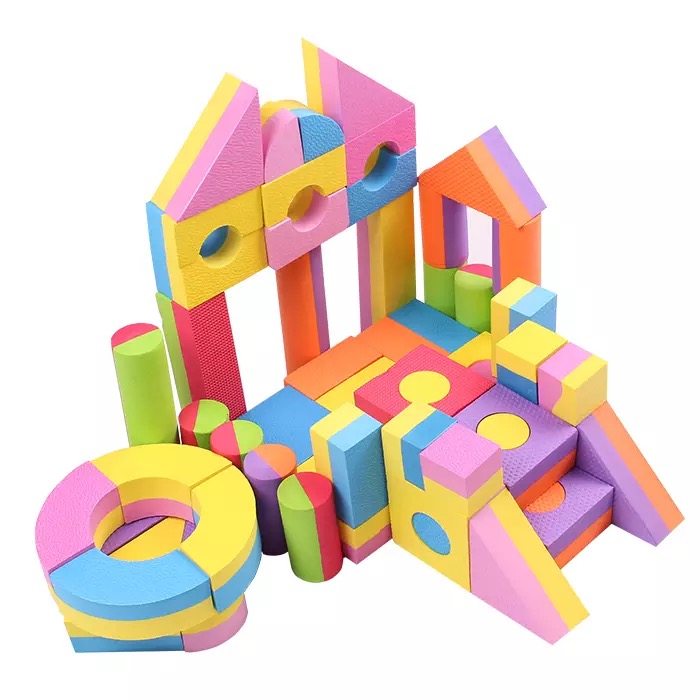
The blocks are easy to store and carry cause it is packed with a PVC bag with zipper. Also after a long time of playing, the blocks can be cleaned easily with water thanks to its closed cell foam.
Eva Twin Colors Building Blocks
Eva Twin Colors Building Blocks,Twin Colour Building Blocks,Colorful Child'S Building Blocks,Colors Kid Building Blocks,Kids Building Eva Block,Eva Educational Building Blocks
Huizhou Melors Plastic Products Factory , http://www.melorsfoam.com