Editor: With the increasing awareness of environmental protection and the gradual improvement of environmental laws and regulations, the problem of pump leakage has drawn more and more attention. In theory, the most effective measure to prevent pump leakage is to use a sealless pump. "On the magnetic pump and shield pump," a paper focuses on the two types of sealless pump that is magnetic drive pump, shield pump basic principle, performance, scope of application and its advantages and disadvantages, and two kinds of pumps were compared. For many years, the conventional sealed pump has been the main equipment of the petrochemical industry. This pump contains a wide range of seals, from packing seals to complex double-ended mechanical seals. The main advantage of a sealed pump unit cost is low, the versatility of the design, the user has customary maintenance methods. The disadvantage is that the seal must create a leak to lubricate the sealing surface. Leakage of packing seal is generally 3 ~ 80mL / h, manufactured a good mechanical seal only a trace leakage, the amount of leakage of 0.01 ~ 3mL / h. If an accident is sealed out, the transport medium leaks into the atmosphere, thus jeopardizing the person and the environment. In addition, while mechanical seals and their sophisticated assistive systems have become more and more complex, the progress made in extending the service life of seals has not always been satisfactory. Therefore, a viable and important option is to use a centrifugal pump that does not require a shaft seal, a hermetically sealed pump. In contrast, a sealless pump can greatly reduce or eliminate the hazards of such catastrophic accidents and greatly extend the service life. Sealless pumps mainly include magnetic drive pump and shield pump, the structure is only static seal without the dynamic seal, used to transport liquid can guarantee a drop of leak-proof. 1. Magnetic drive pump Magnetic coupling drive pump (referred to as magnetic drive pump) was first developed in 1947 by the British company HMD Geoffrey Howard. A few years later, Franz Klaus of West Germany also succeeded in developing one after another. The first companies to use magnetically driven pumps were Imperial Chemical Industries in the United Kingdom and Bayer Chemical in Germany. The primary purpose of developing a magnetically driven pump was to protect the safety and health of people working in industrial, chemical, nuclear, and defense industries. Since the mid-1970s, due to the development of a new generation of permanent magnet and silicon carbide bearing technologies, such as rare earth cobalt (1978) and the most powerful neodymium iron boron (1983), the technical level of magnetically driven pumps has been greatly improved . According to foreign samples and literature data, the flow rate of the magnetically driven pump can now reach 1150m3 / h; the lift reaches 500m; the medium temperature range is -120 ℃ ~ 450 ℃; the viscosity limit is 100-200cp; the abrasive solid content in the medium can reach 1.5 % (By weight), the solid particle size up to 100μm; take special measures, the pump can transport 20% insoluble solids in the slurry, the solid diameter of up to 20mm; system pressure up to 450bar. Magnetically driven pumps are also adapted to the high vacuum conditions that mechanical seals can not handle. These technical breakthroughs and other improvements make the magnetic drive pump reliability and economy have astonishingly improved. Investigation of the availability and ease-of-maintenance of magnetically-driven pumps and mechanical seal pumps showed that the rate of damage and failure of sealed pumps was significantly higher than that of magnetically driven pumps. For example, an average life of 6 months for a mechanical seal on a hydrothermal pump at 400 ° C, whereas a magnetically driven pump can operate for many years, the only maintenance required is for proper lubrication of the external bearings of the pump and the motor. The wealth of experience gained in the chemical industry has led to the conclusion that magnetically driven pumps have become the most economical solution to many process installations. Therefore, the use of magnetically driven pumps has increased not only because of a reliable environmental factor, but also significantly reduces the economic factors of operating and maintenance costs. Its range of applications has expanded from the delivery of hazardous liquids and valuable liquids to common pump applications where long life and low maintenance are required. For example, offshore vessels are driven by magnetic pumps to transport cold water for air conditioning systems due to high maintenance costs. The rapid growth in use of magnetically driven pumps in the last decade has become a common fixture in a variety of applications. Magnetically driven pumps now cover 90% of all applications in sealless pumps. Magnetically driven pumps use magnets to attract ferromagnetic materials and the magnetic or magnetic field between the magnetic properties of non-ferromagnetic material does not affect or seldom affect the size of the magnetic force, it can be non-contact through the non-magnetic conductor (isolated Sets) for power transmission, this drive known as the magnetic coupling. Motor through the coupling and the outer magnet together, the impeller and the inner magnet together. Between the outer magnet and the inner magnet with a fully sealed isolation sleeve, the inner and outer magnet completely separated so that the inner magnet in the medium, the motor shaft through the magnet pole between the suction force directly impeller synchronization Turn. Its main advantages: Because the drive shaft does not need to penetrate the pump housing, but the use of magnetic field through the air gap and the isolation sleeve thin-walled transmission torque, driven by the inner rotor, thus fundamentally eliminating the shaft seal leakage channel, to achieve a complete seal ; Overload protection when transmitting power; in addition to magnetic materials and magnetic circuit design have higher requirements, the remaining part of the technical requirements are not high; magnetic drive pump maintenance and repair workload is small. Its main drawback: magnetic drive pump efficiency lower than ordinary centrifugal pump; anti-single-sided leakage isolation cover materials and manufacturing requirements; magnetic drive pump due to material and magnetic transmission restrictions, so the domestic general only for transportation 100 ℃ the following, 1.6MPa below the media; As the isolation sleeve material wear resistance is generally poor, so the magnetic drive pump is generally used for conveying medium without solid particles; Coupling requirements of high, right in the wrong, Can lead to damage to the bearings at the inlet and to the wear of the one-sided leak isolation sleeve. 2. Shielding pump Shielding pump is a centrifugal seal pump, pump and drive motor are enclosed in a pumped medium filled pressure vessel, the pressure vessel is only static seal. This construction eliminates the need for rotary shaft seals in conventional centrifugal pumps to be completely leak-free. Shield pump pump and motor together, the motor rotor and pump impeller fixed on the same axis, the shield sleeve motor will be separated from the stator and rotor, the rotor is transported medium, the power through the stator magnetic field Pass to the rotor. Its main advantages: ①compared with a sealed pump, eliminating the need for maintenance and replacement of the seal of the trouble, but also eliminates the coupling, a small number of parts (mechanical seal pump only about 30%), high reliability. No rolling bearings and motor fan, do not need to add lubricating oil, and smooth operation, low noise. Configurable bearing wear monitor to detect bearing wear. ② compact structure, small footprint, low requirements of the base and the base, there is no coupling of the problem, easy to install and low cost. Routine maintenance workload, low maintenance costs. ③ In the vacuum system or "vacuum" and "positive pressure" alternating operation of the normal operation without leakage. The material can be fed directly from the vacuum tank to other vessels under high vacuum conditions. Wide range of use, for high temperature, high pressure, low temperature, high melting point and other conditions can meet the requirements. The main drawbacks: ①due to the use of sliding bearings, and with the media being transported lubrication, so the poor lubrication of the media is not suitable for shielded pump delivery. Generally suitable for shielding pump medium viscosity range of 0.1 ~ 20cP. ② shielded pump efficiency is usually lower than a sealed centrifugal pump. However, in the case of medium and low power, compared with the double-end seal pump, the latter has little difference in overall efficiency due to the increased power consumption of the cooling and flushing systems. ③ centrifugal pump operation, the required flow should be higher than the minimum continuous flow. This is especially important for shielded pumps because at lower flow rates, the pump is less efficient and can cause heat to evaporate and cause the pump to dry and cause damage to the plain bearings. 3. Comparison of magnetically driven pumps and shielded pumps Magnetically driven pumps have become common equipment in a wide range of applications over the past decade. In contrast, shielded pumps have been seen as a higher price, more special pump, in most cases only when there is a special order to design and manufacture. Although this view is changing with the advent of standardized shielded pump families, shielded pumps still account for a relatively small share of the market. In general, the reliability of a hermetic pump is equivalent to or better than a comparable hermetic pump. However, both types of pumps are easily damaged due to improper use, especially dry running and deviating from the design point. Bearing-free lubrication of the bearings with a transmission medium pump after a long period of dry-bearing wear occurs. In the absence of operational monitoring, this wear is invisible and can in some cases result in damage to the pump and rupture of the gland. Standard magnetic drives can cause fluid to leak into the coupling body in the event of damage and leak through the coupling bearings to the outside atmosphere. This leakage is usually controlled by the liquid that must flow through the tortuous path, generally without serious consequences. This standard magnetic drive can also be greatly improved to avoid leaks by improving the method of venting to prevent pressure build-up on the coupling body and the use of an auxiliary (drive) shaft seal to prevent leakage. In contrast, shielded pumps seal the fluid in the motor body and prevent further leakage. However, to seal the fluid, it is only possible with close attention to the cable glands between the pressure vessel (motor housing) and the terminal box. This site has always been the only weakness shielding the pump. Bad design will make the second (referring to the motor shell) sealed with no effect. Even if the gland is damaged, the magnetically driven pump can be completely cleaned and undamaged parts can be reused. This maintenance can be done on site if necessary. Leakage to the shielded pump motor body can cause damage to the windings. Although some pumps have a detachable stator structure, most shielded pumps use hermetically sealed motors or have welded structures that need to be sent to the factory for repair or replacement of an expensive body component. For standard magnetically driven pumps, there is no need to approve hazardous areas for use, while shielded pumps require a certificate of conformity. In many cases, these certificates are also inconsistent with each other in European countries and may require the addition of operating condition monitoring devices, such as level probes that require process fluid storage. For the standard form of shielded pump, the temperature is limited to about 100 ℃. The deciding factor is the degree of insulation used for the motor windings. To overcome this problem, the motor is equipped with an independent cooling circuit, which increases the additional cost of piping, coolant supply, pumps and heat exchangers. Standard synchronous magnetic drive pump can operate at about 400 ℃ temperature. In general, magnetically driven pumps can meet 90% of all applications for hermetically sealed pumps. This pump specifications complete, affordable, short delivery time, easy to use, do not need to repair electrical workers involved, but also with the ordinary seal pump direct exchange. Shielding pump structure is complex, expensive, usually can not meet the conventional standards. In addition, sealing parts involved in maintenance issues, multi-species installation problems, and delivery problems such as long, which makes the shield pump can only be used in magnetic drive pumps can not meet the high degree of danger of a variety of edge applications. It is easy to see that although these two kinds of pumps occupy the market at the same time, magnetic drive pumps will occupy a larger market share and become the main equipment for various environmental protection and safety industries in the future. In China, because people's awareness of environmental protection is not yet very strong, environmental laws and regulations are still not sound enough
Led Grow Lights For Herbs
We have full spectrum LED cannabis grow lights for a multitude of applications including: urban farming, hobbyist growing, aquariums, animal cages or environments and even happy lights! These lights are versatile and easy to use for all of your organic needs.
LED Grow Lights are very popular among cannabis growers as an alternative to HPS grow lights. They tend to run cooler and also usually come with built-in cooling. They can often be plugged into a wall and simply hung over plants which is definitely easier than setting up an HID Grow Light. LEDs also have great penetration so they don't need to be moved frequently like fluorescents.
Main Features:
Upgraded Epistar chips,High Lumen,High penetration.
Zener Diode protection Each LED,one LED Out,other LEDs still work.
High quality material,Listed Certification Wires,Heatproof Tube,Zero-Risk to catch fire.
Efficient Full spectrum Special rations of Blue,Red and White for both blooming &fruiting stages.
Adopting isolated power supply,safe&easy to maintain&long life time.
Aluminum heat-conducting plate+high quality brand fans,efficient heat dissipation.
IR LED involved,it is not as bright as other leds,But promote the yield.
Plug with listed certificate safe to use.
Item Display
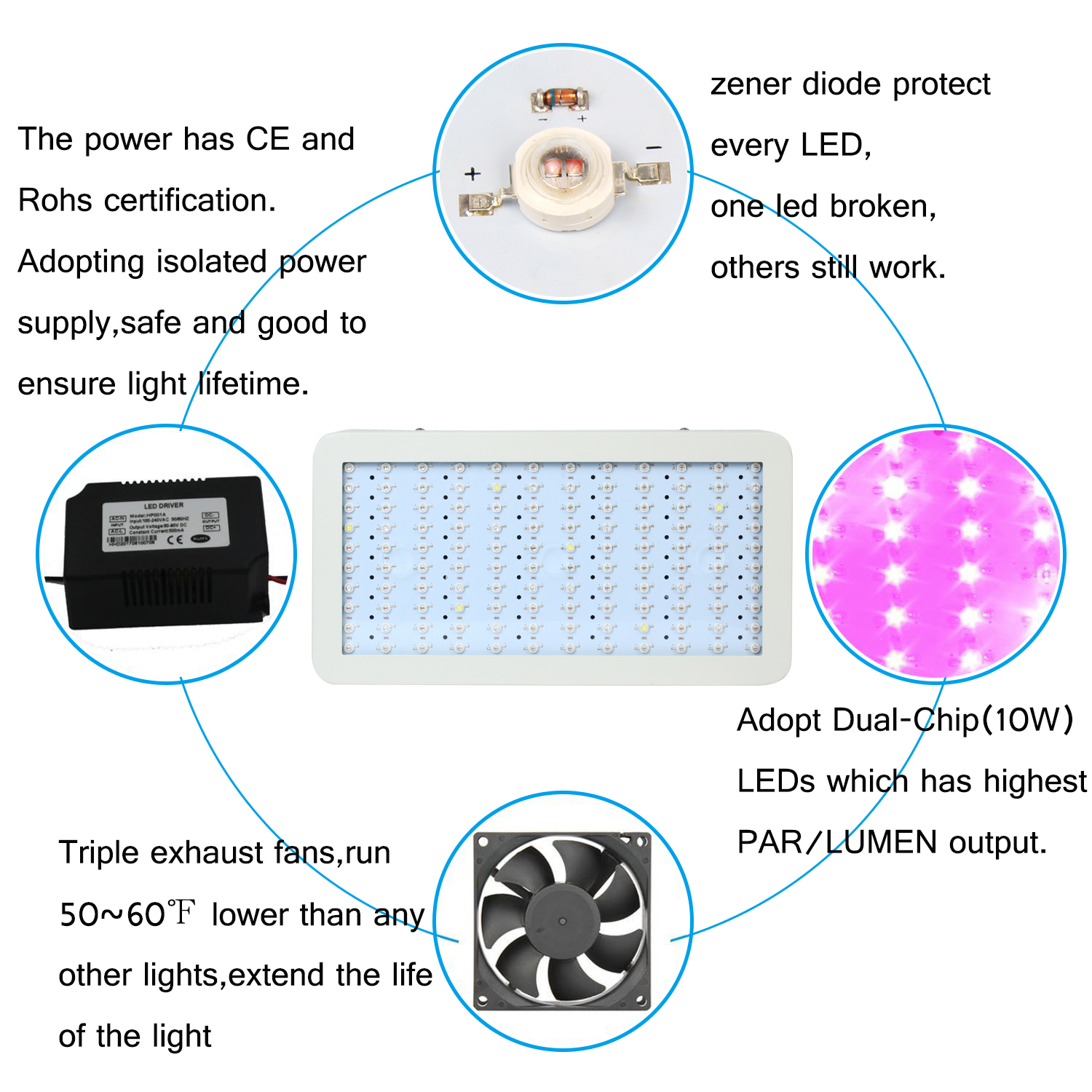
The Plug of LED Grow Lights you can use
Application:
Ideal for all phases of plant growth, and works well with water solution culture and soil culture.Can be used in house garden,pot culture,sowing, breeding farm,flower exhibition,bonsai garden,green house,sowing farm,greenhouse cultivation,water soluble breeding, pipeline cultivation and so on.
Quality Control systems and after-sales
Package
Philizon have over 6 years' experience in designing and manufacturing led grow lights. Persuiting to offer the best grow lights for plants growth, we cooperate with the scientific research institutes and the Academies of Agricultural Sciences in USA, Australia anada, UK and so on.A great number of commercial plant growers test the lights, and their feedbacks show that this lamp owns a lot of 640nm,660nm and 740nm lights, which gives the plants enough nutrient in the flowering and fruiting phase and bring a far higher yield than other led grow lights in the market.
Trade Terms
Payment: T/T, L/C, Paypal, 30% deposits before production, 70% balance to be paid before deliverying(Western Union are welcome)
Sample will be delivered within 7 working days.
Discounts are offered based on order quanlityes.
MOQ:sample order are acceptable
Delivery ways:DHL,UPS,FedEx,TNT, door to door,by sea,by air,etc.
Led Grow Lights For Herb,Led Grow Light,Double Chips Led Grow Lights,2000W Led Grow Light
Shenzhen Phlizon Technology Co.,Ltd. , https://www.szledaquariumlight.com