A turbocharger is an energy-efficient component that is mounted on an engine and uses the energy of the engine exhaust gas to compress the air and increase the engine intake by increasing the intake air amount of the engine. With the implementation of Euro IV and higher emission standards in China, turbocharged engines will become increasingly popular.
Supercharger noise hazard
The maximum speed of the supercharger can reach 300,000 r/min. Due to the interaction between the impeller and the airflow, the dynamic imbalance of the rotor and the nonlinear oil film force of the bearing, the supercharger generates various noises during use. At present, in China's cities, when a supercharged truck or bus passes, the passerby will hear the whistling of the supercharger. Therefore, supercharger noise has become an important source of environmental noise pollution. High frequencies mean short wavelengths, so booster noise is more likely to propagate into the car with a small attenuation rate through various gaps, causing noise interference to the driver and passengers. Supercharger noise is usually high-frequency harmonics, which will greatly reduce the acoustic quality of the car, so the control of supercharger noise is an urgent matter.
Vibration and noise reduction solution
In order to reduce the vibration and noise of the supercharger and improve the overall performance of the supercharger, our company has attached great importance to the supercharger noise and vibration control in recent years. The special experts lead the core technical team to carry out the core technology of the supercharger (including noise, Vibration, sound and vibration roughness, referred to as NVH). Train NVH engineers to analyze noise vibration problems and propose optimized solutions for products. A vibration test room was established, a noise acquisition and analysis system was purchased, and relevant engineering and technical personnel were organized to carry out technical training. Up to now, our company has built a shaft trajectory test system (see Figure 1), a laser vibrometer (see Figure 2), a portable noise and vibration signal acquisition test system (see Figure 3), and an electric vibration test system (see Figure 4), as well as the test vehicle, dynamic balancing machine and other related equipment, can complete the shaft trajectory test of the supercharger rotor, the natural frequency test of the supercharger rotor and the blade, the turbocharger vibration and the vehicle NVH Performance tests, reliability testing and evaluation of supercharger parts. At the same time, our company is setting up an anechoic chamber, which can measure the supercharger noise according to international standards in a test room under certain acoustic conditions, eliminate other noise and environmental interference, and find the noise source in a targeted manner. At the same time, record the operating parameters of the supercharger, pressure ratio flow, etc., and correlate with the noise to obtain the Noise Map (see Figure 5).
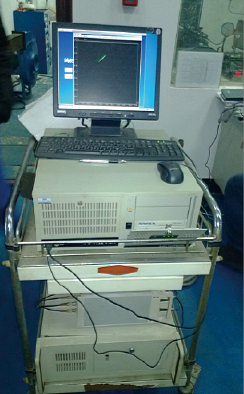
Figure 1 Axis Trajectory Test System
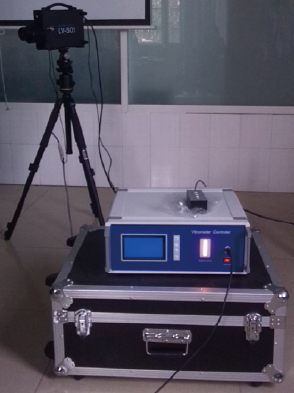
Figure 2 Laser vibrometer
Under the leadership of experts, the work of supercharger noise and vibration has made a big breakthrough. The technicians have a clear understanding of the mechanism, frequency range and propagation path of the supercharger noise. In the process of processing supercharger noise, several types of supercharger noise are summarized: synchronous noise due to excessive rotor imbalance at high speed; secondary synchronous noise due to half-frequency whirl in floating bearing system The vortex generated by the position of the closed gas bypass valve port, the discharge bypass noise generated when the frequency is close to the natural frequency of the cavity; when the compressor flow is too small, the airflow at the vane diffuser and the inlet of the working wheel The wall surface is separated to generate airflow vortex surge noise and the like. In view of the above problems, we propose to control the rotor dynamic balance VSR (Vibration Sorting Rig) G value; optimize the inner and outer gaps of the floating bearing and the rotor and the intermediate; change the cavity size to make its natural frequency away from the frequency of vortex release; modify the impeller Design, pressure relief valve control, VNT and EGR joint calibration, so that the engine operating curve away from the surge line and other turbocharger damping, noise reduction program.
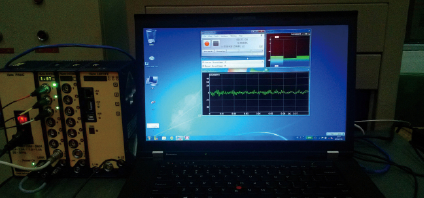
Figure 3 signal test acquisition system
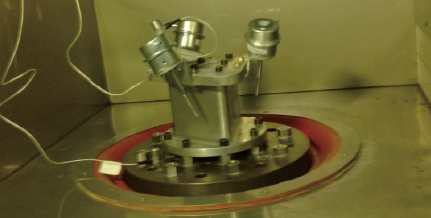
Figure 4 Shaking table
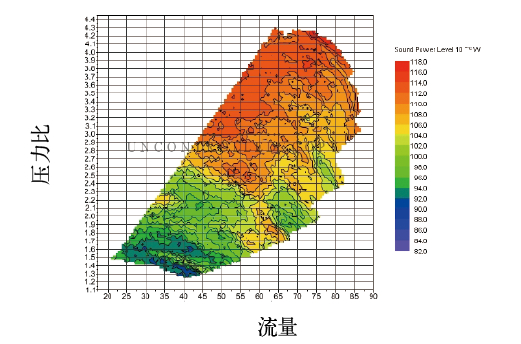
Figure 5 noise spectrum
Aiming at the noise radiated by the supercharger pipeline vibration, it is proposed that the method of rectifying the pipeline is more effective than rectifying the supercharger. The vibration value of the turbocharger-related position is tested for each engine type of the engine. The vibration data is processed by Artemis or Matlab, and the relationship between the RMS and the time of the turbocharger vibration acceleration under the corresponding working conditions is obtained (see Figure 6). Pressurer Campbell diagram (see Figure 7). This information can be used to analyze the vibration acceleration of the engine and supercharger as well as the excitation source for easy control and noise and vibration. In response to the noise problem in a certain host factory, we specially sent NVH engineers to test the supercharger noise and analyze the reasons, use the portable noise recording equipment to record the on-site noise sound pressure time history, use the corresponding analysis software or write the program to diagnose the noise source and spread. The way to confirm whether the noise is acceptable (using the principle of sound quality) and successfully solve the noise generated by the supercharger.
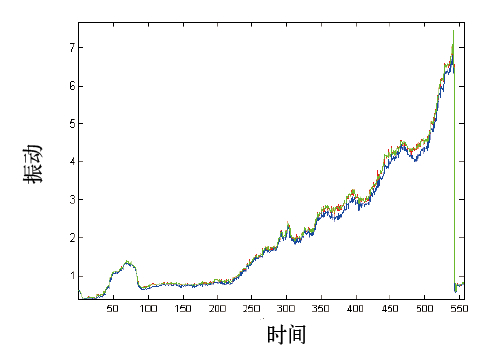
Figure 6 Vibration RMS versus time
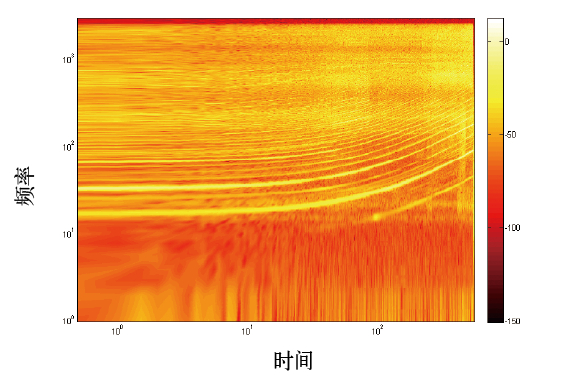
Figure 7 Campbell diagram of the turbocharger in one direction
Conclusion
The NVH level of our company is gradually improving, and the relevant supersonic noise vibration mechanism is gradually improving, and relevant solution optimization solutions are being implemented. It is believed that through the continuous efforts of our team, we will use existing equipment and knowledge to improve the NVH performance of our turbocharger products, provide a basis for the development of relevant theoretical and predictive methods, and provide data and implementation for establishing supercharger noise vibration standards. These standards provide a means of testing.
High accuracy load cell, produced by Shandong Jinzhong Science & Technology Group Company Limited according to OIML R60 International Recommendation, has advanced structure, exquisite technology and excellent quality, reaches modern international level, and has high reputation at home and aboard. At present, the company can provide over types and 300 specifications of high accuracy load cell with capacity from 10kg to 500t to the customers, which are widely used in weighing and force measuring fields.
Mini Load Cell,Load Cell,Column Digital Load Cell,Shear Load Cell
SHANDONG JINZHONG SCIENCE & TECHNOLOGY GROUP COMPANY LIMITED , https://www.chinagoldbell.com