The medium frequency induction furnace has the outstanding advantages of high melting speed, high efficiency, easy temperature control and environmental protection. It has become the main melting equipment for casting enterprises to produce castings, but the service life of the furnace lining has become a difficult problem affecting the early quality and enterprise benefits of castings.
After years of production practice, our company launched the solution of “forming furnace lining + electric building furnace constructionâ€, completely abandoning the backward process of hand-made lining, avoiding the influence of human factors. At present, the 25-5000kg electric furnace forming furnace lining has been applied in the production of thousands of casting enterprises at home and abroad, and is widely adapted to smelting black and non-ferrous metals and various alloys thereof, and has achieved good economic benefits.
Forming furnace lining
Molding lining refers to a lining of a fixed-size refractory material that is mechanically produced and industrially mass-produced. It has the advantages of large bulk density, high strength, good material quality, uniform particle size, and good consistency of finished products, which can not be compared with the furnace lining in the furnace. The forming furnace lining is made of high-purity corundum Al2O3 and fused magnesium MgO as the main substrate. Since the sintered layer of magnesium aluminum spinel or aluminum-magnesium spinel is formed during the smelting process, the forming lining has excellent thermal stability, is not susceptible to thermal shock cracking, has excellent high temperature resistance, and is not susceptible to slag corrosion. specialty.
The dimensions of several typical forming furnace linings and corresponding intermediate frequency electric furnace induction coils are shown in Table 1.
Table 1 molding furnace lining model and corresponding induction coil size

Note: The data comes from the Penguin brand catalogue of Shenyang Hengfeng Industrial Co., Ltd.
The advantages of forming furnace lining are as follows:
(1) Easy installation, saving time and effort (only about 20% of the lining time in the furnace).
(2) No need for oven, energy saving (saving fuel costs, saving more than 15%).
(3) Fast melting and improved efficiency (the active power is increased, and the melting time is shortened by about 10%).
(4) The molten steel is pure, reducing the inclusions (preventing the refractory material from entering the melt and causing inclusions and reducing the pores).
(5) No need to make up the furnace, the maintenance is simple (only the plastic material is used to smear the seam, that is, the smelting is not required to wait).
(6) The furnace age is longer and the liquid output is large (100 steel furnaces or more for steelmaking and more than 200 furnaces for copper smelting).
(7) High safety, avoiding the furnace (using a double-layer lining composite structure to effectively prevent steel penetration).
(8) The life is stable and it is easy to arrange production (the life consistency is good and the production schedule is convenient).
(9) Reducing emissions and being environmentally friendly (the lining can be reused and the discharge of solid waste is reduced).
2. Benefit analysis
Application companies are very concerned about the benefits of using the forming furnace lining. The 250kg and 500kg medium frequency electric furnaces are used as examples for comparison. The electricity fee is calculated at 0.8 yuan/kWh and is for reference only.
Case 1: 250kg medium frequency induction furnace (induction coil inner diameter is 450mm). Each forming furnace lining is calculated by using 100 furnaces (actually 120 to 150 heats can be used).
(1) It takes about 4 hours for the 2-3 workers to work in the furnace to save the furnace. With the molding lining, two workers can work for 30 minutes. Can save one worker and 3.5h working hours.
(2) No-burning furnace power-saving Manually pumping the furnace lining oven in the furnace body generally starts from 40kW, gradually rises to 80kW, and needs to be oven for 10~16h. The use of a shaped lining eliminates the need for oven operation. If the average power transmission 60kW oven is calculated for 10h, it can save 600kW·h, and it is calculated by 0.8 yuan per kilowatt hour, which is equivalent to 480 yuan.
(3) The amount of molten steel is large, and the lining of the furnace lining is generally about 230kg (the later use, the capacity is slightly larger). After the forming furnace lining, the first furnace molten steel is more than 280kg, and each furnace has 50kg of steel. Generally, smelting 1t steel consumes 800kW·h. If more than 100 furnaces smelt 5t steel, the converted electricity is 4000kW·h, saving RMB 3,200.
(4) Energy consumption reduction The manual power supply of the hand-made lining is 160kW, and the average melting time is about 1.5h. The use of a shaped furnace lining can reduce the power to 120-130 kW, while the smelting speed is faster and the molten steel heats up faster. Assuming that the two furnaces are fused with molten steel, the highest power transmission time is 1h, and the electricity cost for the 100 furnace is 2,400 yuan.
(5) The lining that is manually milled in the furnace without repairing the furnace must be repaired several times during use to extend the service life of the lining. This wastes refractory materials and delays the smelting time, and the effect of the lining is also not satisfactory. After the forming furnace lining, there is no need to replenish the furnace, which improves the smelting efficiency.
(6) Improve the quality of molten steel, avoid the accident of wearing the furnace. Because the forming furnace lining is made of high-quality refractory materials and special processes, the bulk density is high, the surface strength is high, and its erosion resistance greatly exceeds the hand-made lining. Therefore, the molten steel melted by the forming furnace lining is much less, and the quality of the molten steel is also reliably guaranteed. At the same time, the furnace accident can be avoided because the forming furnace is lined with a safety lining as a protective layer.
Case 2: The benefits of the 500kg intermediate frequency furnace (induction coil inner diameter 550mm) after forming the furnace lining are shown in Table 2.
Table 2 Comparison of Benefits of 500kg Medium Frequency Furnace after Forming Furnace Lining
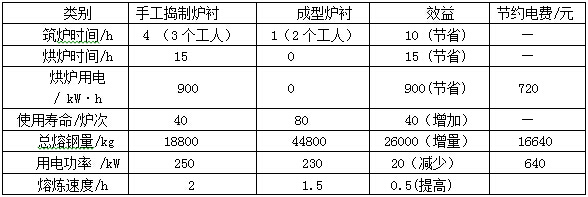
Note: The inner diameter of the induction coil is 550mm.
It can be seen from Table 2 that the 500kg medium frequency induction furnace saves electricity by 18,000 yuan only by oven, multi-melting steel and reducing electricity consumption.
In summary, the electricity cost saved by using the forming lining is greater than the cost of purchasing the forming lining. Reducing the number of furnaces is also reducing the input of raw materials and labor. The more you use, the more obvious the effect. Therefore, the forming furnace lining is a highly efficient power saving product.
3. Forming furnace lining installation
The forming furnace lining is embedded in the beating layer as shown in the drawing.
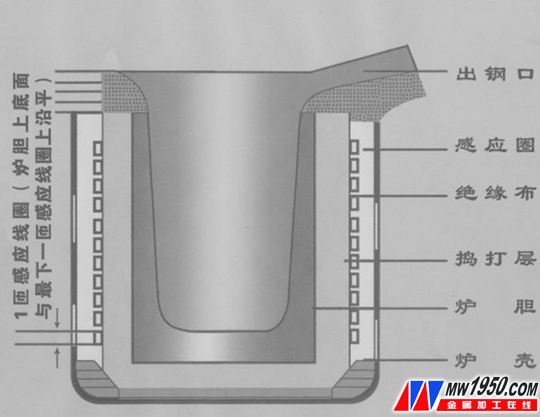
Forming furnace lining installation diagram
As can be seen from the drawings, the forming lining and the backing ram layer form a complete lining. Since the backing layer is always in a non-sintered state, the wave type thermal shock generated during the smelting process can be buffered, so that the lining does not expand and crack, thereby protecting the integrity of the lining, so it is called a safety lining. The double-layer composite lining has an adaptive adjustment capability of volume deformation, that is, stress buffering capability.
4. Electric furnace building machine
In the application practice of the forming furnace lining, the phenomenon that the transverse crack occurs at the joint of the side wall and the bottom of the forming lining and the lining is prematurely invalidated, the larger the capacity of the furnace body, the more prominent this phenomenon. The reason for this phenomenon is mainly due to the fact that the beating layer is not tied tight during the installation of the forming lining. Unfavorable factors such as poor installation environment and high labor intensity of workers are difficult to overcome. In order to solve this problem, our company has developed an electric building machine with reference to foreign advanced technology (see Table 3 for main performance parameters). The use of electric furnaces can reduce the labor intensity of workers, improve labor efficiency, and ensure the firmness of the beating layer.
Table 3 Main performance parameters of portable electric building machine
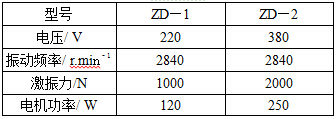
The vibration force generated by the motor driving the eccentric wheel transmits the vibration force to the sand through the vibrating fork at the front end, so that the sand material is tightly packed and the air in the sand is excluded to achieve a higher filling density. The installation of the forming furnace lining requires dry construction, which can prevent the lining from being damaged by moisture intrusion caused by the lengthy oven dehumidification process during wet knotting.
5. Coil coating
In the application practice of forming furnace lining, many users have found that mica sheet insulation layer, asbestos cloth insulation layer, stainless steel wire mesh alarm layer, waste lining and slipping asbestos cloth layer are used as multi-layer protection structure, which is labor-intensive and difficult. It is recommended to use coil coating to ensure the tightness of the beating layer. After the coil coating protective layer is applied once, it can be used for a long time. The protective layer has excellent thermal insulation performance, which can maintain a large temperature gradient difference between the inside of the furnace and the coil, which is beneficial to prolong the furnace age and maintain the vertical concentricity of the coil and the spacing of the coil turns, and effectively prevent the coil from being deformed. The leakage leakage melt burns the coil. In addition, due to the elimination of asbestos cloth, it is also conducive to environmental protection.
6. Conclusion
The forming furnace lining is made of high-purity corundum Al2O3 and fused magnesium MgO. It has a series of advantages and is widely used for melting black, non-ferrous metals and various alloys. The dry construction of the electric furnace building machine enables the rapid and reliable installation of the forming furnace lining, and greatly improves the service life of the lining, and has broad application prospects.
It is expected that with the widespread use of quick-fit forming furnace linings, a profound revolution will be brought to the lining application of coreless induction furnaces.
Shenzhen You&My Electronic Technology Co., Ltd , https://www.ymledtrade.com